National Center For Manufacturing Sciences & US Army Research Laboratory Are Collaborating
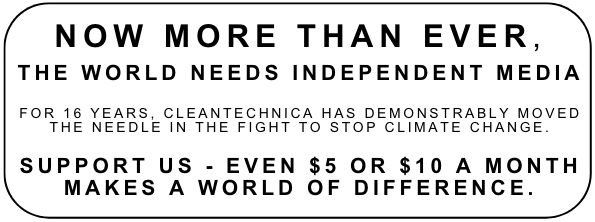
The National Center for Manufacturing Sciences (NCMS) and the US Army Research Laboratory in Aberdeen are collaborating to launch the Advanced Manufacturing, Materials, and Processes (AMMP) program. The new program is intended to support US manufacturers with their large-scale additive manufacturing (3D printing) projects. Cosima N. Boswell-Koller, Ph.D., NCMS Senior Project Manager and AMMP Program Lead, answered some questions about the program for CleanTechnica.
1. Why did the National Center for Manufacturing Sciences (NCMS) and the Army Research Laboratory (ARL) decide to collaborate?
NCMS has over 30 years of experience creating and managing collaborations across industry, academia, and government. The Advanced Manufacturing, Materials, and Processes (AMMP) Program was created to advance the state-of-the-art in additive manufacturing technology and accelerate its transfer. Our streamlined approach offers ease, flexibility, agility, and engagement. The result is a high adoption rate and each stakeholder sees immediate impact from their work. NCMS works with over 105 members and 400+ partner organizations with a swift on-boarding process that allows us to stay ahead of emerging needs.
2. How will AMMP help US manufacturers be more competitive?
As a membership organization, NCMS brings together the right people to identify, evaluate, and solve a problem. The combination of long-established relationships, a stellar reputation, and credibility with manufacturers of all sizes gives us the collaborative power to partner small R&D companies with top-tier OEMs. The results are innovations and opportunities to develop, refine, and provide user-centric solutions that, in turn, help US manufacturers remain at the forefront of global competition. In 2018, the global additive manufacturing market is expected to be sized at 12.8 billion US dollars, and the US is a key player in the technology. We will advance the state of the art in additive manufacturing, make better capabilities available to the end-users contributing economic growth and development in Harford County and the State of Maryland while increasing our member organizations’ manufacturing competitiveness.
3. How will they collaborate in practical terms? Will there be a physical site where meetings will take place, or will there be conferences and workshops?
We are very early in the AMMP Program and exploring numerous possibilities for the collaboration. Currently some of the discussion topics include a physical facility in Aberdeen, Maryland, virtual meetings, online webinars, and technology showcases.
4. What are some of the short-term and long-term goals of the collaboration?
Throughout the AMMP Program, projects will focus on six key technology areas as dictated by the ARL to support their priority areas. These range from essential science and technology, feedstocks for additive manufacturing, real-time process control, through to materials for protection. We will facilitate next-generation manufacturing breakthroughs focused on decreased costs, increased speed, and point-of-need production. Longer term, the AMMP Program will facilitate breakthrough manufacturing solutions in materials and equipment that do not yet exist.
5. Why did they select aluminum alloy as a focus area?
While additive manufacturing uses advanced fabrication techniques, the alloys being used are generally intended to replicate the composition of conventional manufacturing alloys. However, when these alloys are used in additive manufacturing, inherent changes in their properties and behavior have been observed, such as high levels of distortion, anisotropic tensile properties, and defects. Aluminum is of interest due to its use in lightweight materials and general compatibility with existing designs.
6. Why also focus on prototypes, and prototypes for what?
The AMMP Program spans a range of technology readiness levels from basic to applied research all the way through to prototyping efforts. Prototypes will include new machines, new materials, and new processes all in support of the key technology areas.
7. How will they measure the success of the industry collaborations?
Success of the industry collaborations will be measured through the success of the technology transition to the end-user. At NCMS, we will be tracking follow-on projects, as well as using metrics such as return on investment to determine the success of the projects.
8. What is the roadmap for the next 3-5 years?
Implementation of a Technology Advisory Board with representation of all our members will be charged with developing a strategic technology roadmap. They will take into account current and emerging technologies and map them to existing and future needs of the end-user and the manufacturing industry. Through this Board, members will have an opportunity to make recommendations to key stakeholders.
Image Credit: CMitchell, Wikipedia, CC BY-SA 4.0

Sign up for CleanTechnica's Weekly Substack for Zach and Scott's in-depth analyses and high level summaries, sign up for our daily newsletter, and follow us on Google News!
Whether you have solar power or not, please complete our latest solar power survey.
Have a tip for CleanTechnica? Want to advertise? Want to suggest a guest for our CleanTech Talk podcast? Contact us here.
Sign up for our daily newsletter for 15 new cleantech stories a day. Or sign up for our weekly one on top stories of the week if daily is too frequent.
CleanTechnica uses affiliate links. See our policy here.
CleanTechnica's Comment Policy