Steel Is A Major Climate Problem, But We Have Proven Tools
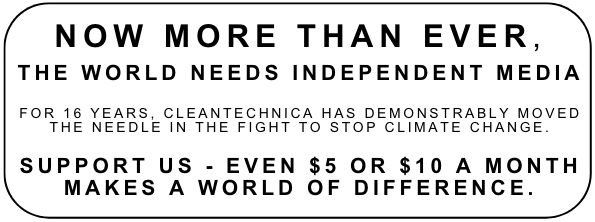
Last Updated on: 3rd December 2023, 09:50 pm
Steel CO2 emissions are about 7% of all global emissions, and steel sucks back about 8% of primary energy globally. It’s a big climate change problem and a big energy consumer. It’s been on my radar for years, but I had prioritized other emissions areas, including transportation, agriculture, cement, and heat. Now it’s made it to the top of my to do list and I spent a bunch of time digging down several pathways somewhat simultaneously in order to understand it better.
Steel is made by alloying carbon and iron in the right proportions, and for variants such as stainless steel with things like chromium. That’s mostly a temperature and mechanical process problem, operating at 1,600° C. That’s actually relatively easy to electrify, as heat at that temperature is fairly trivially easy with electric arc furnaces (EAF), despite remarkable claims such as those of the USA’s new hydrogen strategy that temperatures over 300° C need something to burn. So that part of things is an easy fix. Feed electric arc furnaces with iron and blow oxygen through the mix to get the right carbon levels for steel. That is to say it’s easy technically, but in the messy real world a lot of things intervene.
A lot of steel these days is made from scrap steel, with the addition of some new iron to get the right chemical components in the finished product. That goes through electric arc furnaces too, and so is also highly amenable to decarbonization just by decarbonizing electricity and electrifying transportation. On the average grid today, that has about 0.4 tons of Co2 per ton of steel as electricity hasn’t decarbonized as well as the requirement for about 25% new iron to mix with the scrap steel.
A quick note on these carbon intensities: every single one is subject to lots of variance depending on the process, the fuels, the efficiency, and other factors. These numbers are good enough for orders of magnitude calculations, but there are rather absurd numbers of people working hard to be much more precise about each path way in all its branching diversity.
So we need iron or scrap steel and iron to make steel. But what about turning iron ore into iron? That’s harder. Iron by itself, Fe, doesn’t really exist in nature. That’s because it likes to rust, or rather bond with oxygen. When it bonds with oxygen it loses a couple of electrons. Iron ore of high quality still has a lot of stuff that isn’t oxidized iron, but the oxidized iron is the useful stuff. Getting rid of the oxidation and getting the electrons back in the iron to turn it into pure Fe is a process called reduction.
There are a few industrial processes for reducing iron. A couple are blast furnaces and open hearth furnaces which burn a lot of coal or natural gas to make the iron. Temperatures in the 1,400° to 1,500° C range, very high CO2e emissions, and steel made by this pathway has a carbon debt from 1.2 to 1.7 tons of CO2 for every ton of iron. Not great. The natural gas and steel folks like to claim that natural gas is a win, but it’s really not.
Then there’s direct reduction of iron (DRI), in which natural gas is made into a synthetic gas and at the much lower temperature of 1,000° C the syngas produces carbon monoxide and hydrogen, which reduce the iron ore into 97% pure iron. Much less energy, and much lower CO2 emissions as a result, around 1.0 tons of CO2 per ton of steel (ignoring those pesky upstream methane emissions). It does produce iron with different physical shapes that come out of blast or open hearth furnaces, so the different shape becomes a minor processing issue later.
For those who looked at my charts on aviation and marine shipping, where I started in 1990 and brought historical data forward, then articulated why inductive reasoning from priors wasn’t a good model, my initial efforts in steel will be familiar. What would have been really nice to see and what I was hoping for was a huge growth of electric arc furnaces with scrap metal and direct reduction of iron.

This is a decade by decade view of steel from 1990 to 2020 based on annual reports from the diligent World Steel Association. It’s not a great news story on the surface, but that doesn’t mean that there isn’t good news to be gleaned from it. Let’s pull it apart bit by bit.
First off, volumes of steel manufactured annually have doubled since 1990, so that means it’s pumping a lot more CO2 into the air. Second, the biggest source of growth is in blast furnaces (oxygen) and open hearth furnaces, which are the highest CO2. Yes, the world is making a lot more steel and its higher emissions, a bad combination.
And there’s another bad news story in there. Between 1990 and 2000 the amount of scrap steel processes went up while new steel went down, which makes sense given how much steel we’ve manufactured and is available to scrap. However, after that, new steel from new iron shot up. As a data point, there are about 350 million tons of steel in US fossil fuel pipelines alone, enough for four full years of US production. It’s not like we don’t have a lot of steel. The US has been making about 70% of its new steel from scrap for 20 years or so, so it actually isn’t the biggest part of this problem today, although its historical steel making throughout the Industrial Revolution certainly was, and its only slowly decarbonizing grid isn’t helping.
So where is the new steel being made? Well, historically Japan and the US were #1 and #2 in terms of countries, although Europe added together was very large and possibly #1, but that’s not how the stats are broken out. However, in the past 20 years, China has made increasing amounts of steel every year to feed its massive infrastructure build-out. Roughly 55% of steel is used in building and infrastructure, and the second biggest consumer is the automobile and light vehicle market. All those new cities, 40,000 km of high-speed rail, hydroelectric projects and the like in China needed steel. And China’s car and light vehicle manufacturing has shot up too, with each car on average globally requiring around 0.9 tons of steel, although China does have millions of microcars which use less steel.
India has been accelerating its industrialization too, although to nowhere near the level of China. As a result, #1 and #2 are China and India, with Japan and the US as #3 and #4.
But when we provide this ranking, it’s important to note that it’s really China in the #1 spot and the rest of the world combined at #2. That’s right, China is to steel as the US is to military spending. China manufactures 10 times as much steel as India right now every year. And China took the fastest paths to making steel, high carbon ones, so that’s a problem.
So what the heck is the good news story for steel in this? Well, it has a few components.
The first is that we’ve already manufactured an awful lot of steel. There are hundreds of billions of tons of the stuff lying around, much of it obsolete, much of it temporarily bound into cars and the like, and all of it nicely pre-purified for scrapping in electric steel minimills which will be running off of cleaner and cleaner electricity every year.
The next win is that we’re making about 100 million tons of new steel with direct reduction of iron ore. As a reminder, it has much lower emissions and energy requirements than earlier alternatives. This isn’t a technology in the lab, this is a technology pumping out 5% or so of new global steel.
The next point is that there are a lot of ways to decarbonize direct reduction of iron ore. As a start we can go a step further and make hydrogen and add it to syngas mixes in larger and larger amounts to maximize the reduction results, although this becomes a process which requires external heat to be added. Midrex is going this route and has lower carbon direct reduction working in its technology. They are still using natural gas to provide the heat, but that’s still down to 0.8 tons of CO2 per ton of steel, under half of blast furnace and open hearth emissions.
We could decarbonize Midrex’ process further by using the biomethane we are unintentionally making in landfills and animal dung to create syngas for reduction. There is enough of it that even after we mitigate it as far as possible we are still causing far too much biomethane to be produced, and it’s far better to use it for this than taking sequestered CO2 in the form of natural gas out of the ground. And we could provide the process heat from electricity as well. It’s likely that the Midrex process could cut its emissions down to 0.4 tons of CO2 per ton of steel, around that of scrapping steel in electric arc furnaces.
But then we leave Midrex and syngas direct reduction behind with the HYBRIT process. HYBRIT — short for Hydrogen Breakthrough Ironmaking Technology — is a joint venture between SSAB, LKAB and Vattenfall. It uses biomethane, green hydrogen made from water and green electricity without any fossil fuels, to make iron suitable for shoving into electric arc furnaces with scrap. And it uses zero-carbon iron ore extracted from zero-emission mining, something entirely within the realm of the possible since I was working on a Ring of Fire zero emission mining proposal and a northern Quebec mining wind energy proposal about a decade ago, and something increasingly in place today.
It only requires about 51-60 kg of hydrogen for a ton of new steel, something that has some positive implications for my hydrogen demand strategy through 2100, where the only growth spot is steel. The range is interesting, in that three different sources provide three different numbers, 51, 58, and 60 kg per ton of steel. All are credible, and two are peer-reviewed. I’ve chosen the most recent peer-reviewed number, 51 kg per ton from 2022, as the basis for my assessments going forward.
Lastly, the biggest steel manufacturer in the world is China. And that’s a country which at the present time has proven itself to be radically faster at pivoting and transforming than any jurisdiction with the exception of the narrowly confined geography of Silicon Valley. China has more electric buses, trucks, and trains than any country in the world. China built as much offshore wind energy in 2022 as the rest of the world combined in the previous five years. China is already delivering the cheapest hydrogen electrolyzers. China is both manufacturing more than half the world’s steel, but also more able to decarbonize its steel rapidly.
Hmmm. Only about 25% new steel required with scrap when we arrive at maximum steel circular economy a few decades from now. Only 51 kg of hydrogen for a ton of new steel. Much less primary energy required for electric scrap and DRI processes. China slowing its infrastructure and housing build-out phase. China pivoting to clean steel. But then the Belt & Road Initiative and increasing affluence in India, Africa, and other places to counter that. That’s an interesting set of curves and the basis of another assessment or two.
UPDATE: We reached out to SSAB with a few questions about the HYBRIT process, and the answers to those are as follows:
Q: How much biomethane is used per ton of steel in the HYBRIT process?
A: We’re not using biomethane in the HYBRIT process.
Q: What are the primary remaining concerns about the HYBRIT process in terms of scaling?
A: Innovation is key as this has never been done before on a large scale, and that’s also the challenge: creating something new requires for example bigger electrolyzers. We also need access to fossil-free energy. However, we have proven that the technology works and that steel produced using hydrogen as the reduction agent has the same, if not better, quality as steel made with blast furnace technology.

Sign up for CleanTechnica's Weekly Substack for Zach and Scott's in-depth analyses and high level summaries, sign up for our daily newsletter, and follow us on Google News!
Whether you have solar power or not, please complete our latest solar power survey.
Have a tip for CleanTechnica? Want to advertise? Want to suggest a guest for our CleanTech Talk podcast? Contact us here.
Sign up for our daily newsletter for 15 new cleantech stories a day. Or sign up for our weekly one on top stories of the week if daily is too frequent.
CleanTechnica uses affiliate links. See our policy here.
CleanTechnica's Comment Policy