BMW Group Opening 8 New EV Parts Lines in Leipzig
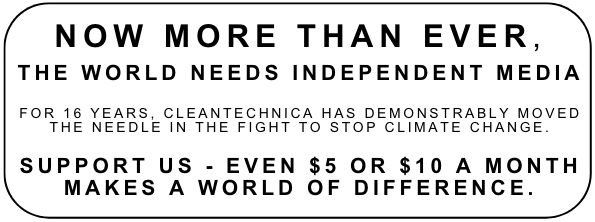
EV battery production gets a lot of attention, and largely because it’s the biggest challenge right now. As more and more EVs get sold, we’re going to have to come up with enough raw materials, refining capacity, and cell production lines–and that’s all before a manufacturer puts the cells in battery packs. But, that’s far from the only difference between an ICE vehicle and an EV. Many production lines for both manufacturers and their suppliers are going to have to either close or shift to make parts useful for EVs.
With all this in mind, you can get a pretty good idea of how serious a manufacturer is about EVs by how many production lines are either getting built or getting retooled for EV components. If they’re doing almost nothing, they’re probably building a few compliance cars. If they’re opening/swapping multiple production lines at a time, they’re making a serious effort.
Fortunately, a recent press release from BMW shows us that it is the serious type, and this is all for battery production alone. Non-battery components are probably a whole other story going on behind the scenes. But, back to its battery component plans:
The BMW Group revealed plans to up its e-component production by eight lines at its Leipzig base by 2024. The news was revealed on 20 October during the Green Day celebration held at BMW Group Plant in Leipzig. In the next year, the two existing battery module lines will be getting a boost with one additional line and five cell coating lines. By 2024, there will also be two new high-voltage battery assembly lines operational. These batteries will power electric models such as the MINI Countryman, which is also assembled in Leipzig.
“The BMW Group has always been a pioneer in the transformation to electric mobility,” said Milan Nedeljković, BMW AG Board Member for Production, “and we intend to remain the leader in the future. Plant Leipzig will be of special importance in this regard, as it’s the birthplace of the BMW i3.”
From 2013 until summer of 2022, Leipzig had manufactured over 250,000 fully electric BMW i3 vehicles and 20,000 plug-in hybrid BMW i8 sports cars. The additional available spaces and the skillsets of its employees will now be devoted to producing e-components. By 2024, more than 1,000 production staff will work in battery component production at Plant Leipzig–700 are working there presently.
“We are working consistently to advance the transformation to electromobility,” said Markus Fallböhmer, Head of Engine at E-Drive Production at BMW AG, “and we continue to develop our e-drive production network to make it happen. From 2024, the entire process chain for high-voltage battery production will run not just at Dingolfing but at Leipzig as well.”
BMW Is Putting Some Serious Money Behind This
This isn’t a cheap effort. BMW’s announcement threw around some big numbers.
The BMW Group tells us that it has invested more than 800 million euros to establish e-component production in Leipzig, which will active by 2020 and occupy around 150,000 square meters on the site. The BMW Group has plans to invest more than 1 billion euros in the Dingolfing Competence Centre for E-Drive Production by late 2022. This investments allows for the production of electric motors. In addition, between 2020 and 2022, there will be an investment of 250 million euros specifically for e-drive component production that takes place in Regensburg.
For the rest of the article, let’s look at what exactly BMW is doing with these investments.
Five New Cell Coating Lines
The first of five new battery cell coating systems will be operational at the Leipzig site by the end of 2023, with another four launching throughout that year. The battery cells will be manufactured by external suppliers to BMW Group specifications. First, the lithium-ion cells will be plasma-cleansed before being coated with specially developed systems for optimum insulation.
A Third Battery Module Line
After being coated, the cells are assembled into larger units known as battery modules. In Leipzig this is done on two existing module lines, with a third set to go live in summer 2023.
Two High-Voltage Battery Assembly Lines
After the battery modules, connectors, control units and cooling aggregates are assembled, they’re placed in an aluminum casing. The number of modules as well as the size and shape of the casing depend on which vehicle model it will be used for so that each car gets a bespoke high-voltage battery. In 2024, two Plant Leipzig assembly lines will also be designated for high-voltage battery production.
A Global Production Network
The BMW Group is utilizing its worldwide production network to meet the rising demand for e-drive component production capacity. High-voltage batteries and battery components for electric vehicles under the BMW and MINI brand will be produced not only in Leipzig but also Spartanburg, USA, and Shenyang, China. With the help of a partner company, high-voltage battery production has been localized at Plant Rayong in Thailand.
The BMW Group is making large investments in electric car technology and infrastructure. In Munich, it has the E-Drive Pilot Plant and the Battery Cell Competence Centre which are constantly improving battery cell production processes. BMW is also launching a Competence Centre for Battery Cell Production just outside of Munich. This new center will allow for the mass-production of high quality lithium-ion batteries at an affordable cost.
Manufacturers at the BMW Group’s Competence Centre for E-Drive Production in Dingolfing produce electric motors, while those at Plant Landshut create casings for the newer, fifth-generation electric drive.
A Solid Continuing Effort
For a full EV transition of the global automotive industry, BMW is obviously going to need a lot more lines. How many? I can’t give you an exact number, but a quick Google search says it builds around 2.5 million cars annually. So, multiply whatever Tesla is doing by around 2.5. That’s a TON of EV production, and a ton of components (well, multiple tons, but it’s a figure of speech).
But, this does show that the company is serious about upping EV production and not just making a few limited-production EVs to satisfy regulatory requirements and give the public a side-show while they crank out even more SUVs.
Featured image provided by BMW.

Sign up for CleanTechnica's Weekly Substack for Zach and Scott's in-depth analyses and high level summaries, sign up for our daily newsletter, and follow us on Google News!
Whether you have solar power or not, please complete our latest solar power survey.
Have a tip for CleanTechnica? Want to advertise? Want to suggest a guest for our CleanTech Talk podcast? Contact us here.
Sign up for our daily newsletter for 15 new cleantech stories a day. Or sign up for our weekly one on top stories of the week if daily is too frequent.
CleanTechnica uses affiliate links. See our policy here.
CleanTechnica's Comment Policy