Who Are The Biggest Electrified Vehicle Battery Cell Producers?
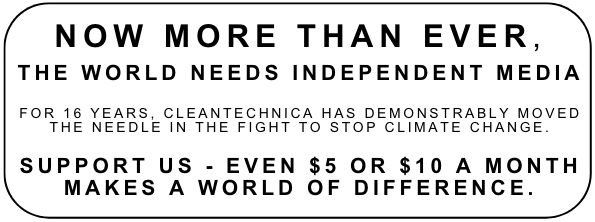
Originally posted on EVANNEX.
By Charles Morris
The good news is that electric vehicle sales are soaring, and the battery business is booming. The bad news is that batteries and the raw materials used to make them could soon become a bottleneck that throttles that growth. More bad news: almost all of today’s EV batteries are made by Asian firms, and it will take years for the US and Europe to catch up.
According to Adamas Intelligence, three million new EVs were registered around the world in 2020, representing 134.5 gigawatt-hours’ worth of batteries. That’s a 40-percent increase over 2019, and the growth trend continues — in the first five months of 2021, the total amount of battery capacity deployed was greater than in all of 2018. Not only are more EVs being sold, but the battery capacity in each vehicle has increased.
A recent article in IEEE Spectrum describes the companies that currently dominate the battery market, and explains some of the technical issues that could shape the race to ramp up production over the next few years.
As of the second half of 2020, six Asian companies supplied 87% of the batteries deployed in passenger EVs.
The biggest battery-builder was China’s Contemporary Amperex Technology (CATL), which supplies Tesla, the Volkswagen Group, Volvo, Stellantis, BMW, Honda and several Chinese automakers. CATL grew by an astounding 3,400% from 2016 to 2020, and accounts for 26% of the global battery market.
In the number-two spot is LG Energy Solution, a Korean firm that supplies Tesla, the VW Group, GM, Groupe Renault, Stellantis and Volvo. It also boasts a 26% global market share.
In the bronze position is Tesla’s long-time partner Panasonic, which also serves Toyota, and has a 17% market share.
![]() |
Next on the list are Samsung SDI (Korea, 7% market share), BYD (China, 7% market share), and SK Innovation (Korea, 4% market share). The remaining members of the top ten are all Asian companies, too.
Tesla is by far the largest customer for batteries — in the second half of 2020, it deployed 22.5 gigawatt-hours’ worth, nearly as much as the next five largest EV-makers combined (BYD, Hyundai, Mercedes, Renault, Volkswagen).
Soaring demand for EVs is putting pressure on the entire supply chain for battery and motor raw materials—prices of lithium, nickel, cobalt, and the rare earth elements neodymium, praseodymium, dysprosium and terbium, have spiked.
The US will need to build some 20 to 40 new battery factories over the next 15 years, with a combined terawatt of new battery capacity, to meet projected demand, Venkat Srinivasan, Director of the Argonne Collaborative Center for Energy Storage Science, told IEEE Spectrum. “Right now, the United States doesn’t have enough materials to do that, so materials substitution and recycling will be key to get this to go.”
That’s what Tesla co-founder JB Straubel has been saying for some time. His company, Redwood Materials, just announced plans to supply battery cell materials from a plant in the US, produced from “as many recycled batteries as available and augmented with sustainably mined material.”
Automakers are not sitting idle. GM is building factories in Ohio and Tennessee with a combined capacity of 70 gigawatts, double that of Tesla’s Nevada Gigafactory. Ford hopes to establish 140 GW of capacity in North America, and 240 GW globally, by 2030, in partnership with SK Innovation.
Technical shifts may help to ease the supply crunch. Lithium iron phosphate (LFP) cells, which tend to be cheaper than those made with NCMA (nickel, cobalt, magnesium, aluminum) chemistries, and use no cobalt, are coming back into style. Elon Musk recently suggested that Tesla would make a long-term shift toward LFP, noting that “there’s plenty of iron in the world.” Ryan Castilloux, Managing Director of Adamas Intelligence, told IEEE Spectrum that the new trend may be for automakers to use nickel-rich chemistries for longer-range or performance cars, and LFP for entry-level models.
Another innovation is “cell-to-pack” construction, which eliminates modules, and arranges prismatic cells directly into packs. Tesla is investigating this technology for its structural battery packs.

Sign up for CleanTechnica's Weekly Substack for Zach and Scott's in-depth analyses and high level summaries, sign up for our daily newsletter, and follow us on Google News!
Whether you have solar power or not, please complete our latest solar power survey.
Have a tip for CleanTechnica? Want to advertise? Want to suggest a guest for our CleanTech Talk podcast? Contact us here.
Sign up for our daily newsletter for 15 new cleantech stories a day. Or sign up for our weekly one on top stories of the week if daily is too frequent.
CleanTechnica uses affiliate links. See our policy here.
CleanTechnica's Comment Policy