UCSD Researchers Devise Low Cost Lithium Ion Battery Recycling Process
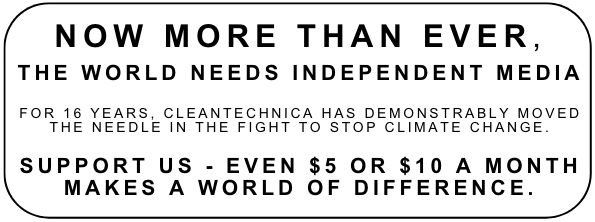
Lithium iron phosphate (LFP) batteries don’t have the highest energy density but they cost less than other lithium batteries and they have fewer issues with thermal runaway. In other words, they tend not to catch fire or explode the way some lithium ion batteries do. Earlier this year, BYD unveiled its Blade LFP battery, which can be punctured, dropped, smashed, overcharged, or overheated without becoming thermally unstable. Tesla Model 3 sedans manufactured in China now feature LFP battery packs. LFP is not the pinnacle of battery technology but it may be just what the EV revolution needs to bring lower priced electric cars to market.
One part of that revolution that needs to be addressed is what to do with old batteries that can no longer power electric vehicles. Experts predict that China alone will generate some 500,000 metric tons of used lithium ion batteries this year. By 2030, the worldwide number could hit 2 million metric tons per year and that may be on the low side as nations begin to adopt policies that will drive the switch to electric vehicles faster. The problem is, recycling at the present time is an expensive and energy intensive process.
Researchers at the Jacobs School of Engineering at the University of California San Diego published a paper in Joule recently that describes a new recycling process for LFP cathodes that uses environmentally friendly ingredients, consumes 80 to 90% less energy, and emits about 75% less greenhouse gases.
Batteries made with LFP cathodes are less costly than other lithium-ion batteries because they don’t use expensive metals like cobalt or nickel. The problem, according to Zheng Chen, a professor of nanoengineering at UC San Diego, is “It’s not cost-effective to recycle them. It’s the same dilemma with plastics — the materials are cheap, but the methods to recover them are not.”
The new recycling process that Chen and his team developed works at low temperatures of between 60 and 80 degrees Centigrade and at ambient pressures. That makes it less power hungry than other methods and the chemicals it uses — lithium salt, nitrogen, water, and citric acid — are inexpensive and not harmful to the environment. “The whole regeneration process works at very safe conditions, so we don’t need any special safety precautions or special equipment. That’s why we can make this so low cost for recycling batteries,” said first author Panpan Xu, a postdoctoral researcher in Chen’s lab.
The researchers first cycled commercial LFP cells until they had lost half their energy storage capacity. Then they took the cells apart, collected the cathode powders, and soaked them in a solution containing lithium salt and citric acid. After they were washed with water, the powders were dried and then and heated. The researchers made new cathodes from the powders and tested them in both coin cells and pouch cells. Their electrochemical performance, chemical makeup and structure were all fully restored to their original states.
Restorative Powers
In use, the cathode undergoes two main structural changes during repeated charge/discharge cycles that lead to a decline in performance. The first is the loss of lithium ions which creates empty sites called vacancies in the cathode structure. The other occurs when iron and lithium ions switch spots in the crystal structure. When this happens, they cannot easily switch back, so lithium ions become trapped and can no longer cycle through the battery.
The process developed by the researchers restores the structure of the cathode by replenishing lithium ions and making it easy for iron and lithium ions to switch back to their original spots. That switching takes place when citric acid is introduced into the process. The citric acid acts as a reducing agent — a substance that donates an electron to another substance. Citric acid transfers electrons to the iron ions, making them less positively charged. That in turn minimizes the electronic repulsion forces that prevent the iron ions from moving back into their original spots in the crystal structure. It also releases the lithium ions back into circulation.
While the overall energy costs of this recycling process are lower, researchers say further studies are needed on the logistics of collecting, transporting and handling large quantities of batteries. “Figuring out how to optimize these logistics is the next challenge,” Chen said. “And that will bring this recycling process closer to industry adoption.”
The Take Away
With old tires and batteries, people used to just throw them into the woods and let nature take its course. If we did something similar with old traction batteries we would created an environmental disaster of epic proportions. Not only that, we would be throwing away many of the raw materials we need to make new batteries, which would be pretty dumb on our part. But unless recycling is cost effective, that’s exactly what will happen. The good news from the UCSD team is that the cost of recycling certain kinds of batteries is going down while the environmental concerns from the process are decreasing as well. That’s a double dose of good news at a time when glad tidings are in short supply.

Sign up for CleanTechnica's Weekly Substack for Zach and Scott's in-depth analyses and high level summaries, sign up for our daily newsletter, and follow us on Google News!
Whether you have solar power or not, please complete our latest solar power survey.
Have a tip for CleanTechnica? Want to advertise? Want to suggest a guest for our CleanTech Talk podcast? Contact us here.
Sign up for our daily newsletter for 15 new cleantech stories a day. Or sign up for our weekly one on top stories of the week if daily is too frequent.
CleanTechnica uses affiliate links. See our policy here.
CleanTechnica's Comment Policy