Take An Inside Tour Of The Gigafactory With Tesla’s JB Straubel
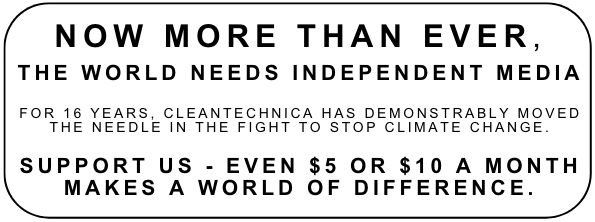
Originally published on EV Annex.
With such enormous interest in the new mass-market Tesla Model 3 electric vehicle, it’s imperative that Tesla Motors [NASDAQ:TSLA] get their massive battery factory, the Gigafactory, constructed and fully operating on a tight timeline. In addition, Tesla’s got significant demand for it’s stationary storage products, the Powerwall and Powerpack, which also depend on heavily on the Gigafactory. To get a ‘Gig’ status update, Lauren Sommer from KQED Science* got an exclusive interview with JB Straubel, Tesla co-founder and Chief Technical Officer, and offers us a rare, inside look at progress.


Sommer writes, “Tesla’s Gigafactory is a lot like Willy Wonka’s Chocolate Factory: it’s mysterious, it’s big and few people have been inside… It’s tucked away in a dusty valley, half an hour east of Reno. Driving up Electric Avenue, the factory is a stark contrast on the horizon. It’s a sleek white building with a red stripe, almost like one of the company’s cars.” In her interview with Tesla’s top brass, Straubel proclaims, “It’s really hard to get a sense of scale. I mean, it’s huge… I think it’s on the order of around a hundred football fields.” Straubel says, the Gigafactory is about scale. He believes scaling up could drive down the cost of batteries 30 percent or more. “We think we’ll probably be able to exceed that,” Straubel says. “Our vehicles can be more affordable. More people can have access to them.”

He talks about the process of baking batteries, “So this is a pretty exciting room,” Straubel says. It’s filled with huge metal tanks, almost like an insanely-large industrial kitchen. “This is where we will actually mix the materials, the raw materials, we mix them into what’s called a slurry.” The main pieces of the lithium-ion batteries, the anode and cathode, are baked by huge machines in yet another room. “It’s a little bit like a giant baking oven except it’s a few hundred feet long,” he says.


Just one room over, the part of the Gigafactory that is running is making something else: the Powerwall. It’s a flat battery, about 4 feet long, 3 feet wide, and it’s Tesla’s first battery for your house. There are stacks of them on the factory floor, ready to ship to customers. “If someone has solar on their house and they install a Powerwall, what this lets you do is store your surplus solar energy,” Straubel says. Homeowners could then use around 7 kilowatt-hours of that stored energy at night, which is several hours’ worth, depending on energy demand. The production floor is also stacked with Powerpacks, a larger version of the battery about the size of a refrigerator. They’re designed to store electricity at factories, industrial sites, or on the grid itself by electric utilities.


So we were wondering — how exactly does a home Tesla Powerwall installation happen? We did some digging and we found this video that showcases some of the install process…
In any event, batteries (for both stationary storage and electric vehicles) are an integral part of Tesla’s strategy according to Straubel. “Batteries are the missing piece in allowing sustainable energy to scale up to 100 percent of our energy needs,” he says. “We’re confident that eventually just about every vehicle on the road will move to being electric. That’s changing the transportation landscape. That’s changing the energy landscape. It is changing the world,” he says.
*Source: KQED Science (article/photos: Lauren Sommer; graphics: Teodros Hailye)
Reprinted with permission.

Sign up for CleanTechnica's Weekly Substack for Zach and Scott's in-depth analyses and high level summaries, sign up for our daily newsletter, and follow us on Google News!
Whether you have solar power or not, please complete our latest solar power survey.
Have a tip for CleanTechnica? Want to advertise? Want to suggest a guest for our CleanTech Talk podcast? Contact us here.
Sign up for our daily newsletter for 15 new cleantech stories a day. Or sign up for our weekly one on top stories of the week if daily is too frequent.
CleanTechnica uses affiliate links. See our policy here.
CleanTechnica's Comment Policy