Using Thermodynamics & 100-Year-Old Technology To Break The $20 Per MWh Barrier
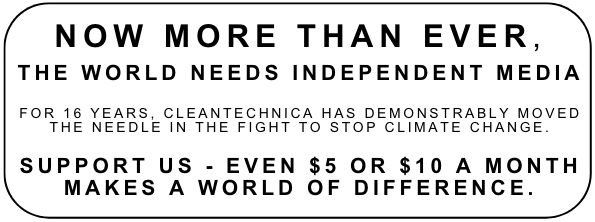
Sign up for daily news updates from CleanTechnica on email. Or follow us on Google News!
This is a guest post by one of our regular, cleantech-obsessed readers, David Fuchs. Clearly, David thinks he’s on to something big. Enjoy the article!
For years, the production of energy has fascinated me. Over the past 20 years, I have experimented with solar cells made via inkjet printer, a hydraulically coupled compressor and turbine based on Tesla’s turbine, vertical wind turbines, high-temperature cracking of water, high COP heat pumps, all the different varieties of Stirling engines, and many other energy projects. Continuously going back to old projects to incrementally improve them and make them perfect has been fun, except perfect is the enemy of finished.
The week long power outage here in New Jersey, after hurricane Sandy, made me realize that we need simple, scalable, cheap, and locally produced power. Removing all distractions and giving an engineer of German lineage a week to think on a problem often gets the problem solved. After pulling out the 7-pocket expanding file with all my past Stirling designs, a couple notepads, my favorite gel pens, a dry erase board, and some reference books, I began designing. As with any engineering project, you need to describe what you want to accomplish, and your limiting factors. Due to cost constraints, engineering is always compromise.
What is the goal? An always-on (24 x 7 x 365) power supply that is inexpensive to produce, can be bulk produced with readily available materials, can be manufactured in any nation using 1950′s or earlier technology, and has a working lifespan greater than 20 years. (That sounds really simple, doesn’t it?)
What are the design criteria?
- Low Temperature Differential (LTD) Stirling based design.
- All parts must be designed for high-speed manufacture and assembly.
- All materials used must be inexpensive and readily available.
- The Stirling design must have the least number of wear points possible.
- It must use inexpensive solar thermal panels for gathering energy.
- The solar panels must be easily produced in an automated fashion.
- It must have inexpensive (dirt cheap) energy storage.
- It must produce at least 3 kW of power continuously (24 x 7 x 365 x 20).
- On a daily basis, it must be capable of gathering two to three times the energy required for a 24-hour period, on the least sunny day of the year. (NREL solar radiation manual)
- It must be capable of storing the energy required for 3 to 5 days of continuous usage with no energy input.
- Any person with basic mechanical skills should be able to install the system.
- The total Levelized Cost of Energy (LCOE) must be under $20 per MWh.
The basic system layout.

This system layout image represents the individual pieces and the energy flows between the individual components. The flow controller controls the heat distribution between components.
The system consists of six main components:
- Solar thermal cells for gathering energy.
- An insulated thermal mass for storing the energy (dirt or water).
- A heat radiator for disposing of waste heat.
- An LTD Stirling engine for generating energy.
- A flow controller for for fluid flow, preventing energy loss from the system, and increasing efficiency.
- An inverter to connect to the grid and convert DC power from the generator to AC usable in your house and power grid.
Each component is designed to be as inexpensive, modular, easily replaceable, and mass producible as possible.
Solar Thermal Panels absorb the sun’s energy in the form of heat. The price for solar thermal panels averages $150 per square meter. Extrude plastic cased panels can reduce the cost to $33-$47 USD per square meter, with slightly lower efficiency.
Thermal Mass is a fancy engineering way of saying “insulated pile of dirt or bucket of water.” This is used to store the heat absorbed through the solar panels. The cost of this varies greatly. It can be dirt insulated all around with hay bales and covered with plastic (~$600 USD), four 2,500 gallon water tanks filled with water or sand (~$4,700 USD), a 9 x 20 shipping container insulated and filled with dirt or sand (~$1,100 USD), or an insulated hole in the ground (~$800 USD). This includes the cost of the aluminum tubing which runs from $1.50 to $2.00 per pound. There should be multiple thermal masses, or zones within a single thermal mass, each filled to thermal saturation in sequence.
Flow Controller is used to transfer liquid to and from each of the components. It is designed to keep as much heat in the system, and reuse the remaining heat as often as possible. When the system is energy saturated, or when there is no alternative, it will dump the energy out via the radiator. The multiple thermal masses or zones, at different temperatures, and external temperatures at different times of day, make waste heat reuse an efficient way to extract as much energy from the system as possible. This will run $150 to $300 USD.
Heat Radiator is used to radiate waste heat from the system, or as a heat sink when the system is saturated. This can be a standard aluminum fin radiator and fan, a cold body of water, a hole or trench in the ground with a pipe running into or through it, or any thing else at a lower temperature. The cost varies with type of radiator.
LTD Stirling is the key to this system. The design uses two separate heating and cooling chambers (upper and lower) with a shared piston. The volume is 9 cubic feet (68 gallons). It has 500 sq ft of radiator surface area (floor area of a large two car garage). It is 6.5 feet tall, 3.5 feet wide, and 3 feet deep. It can be vertically or rack mounted. And it is designed to produce up to 6 kW of power, but will be run at 3-4 kW for greater efficiency. The larger these units are, the greater the radiant surface area. The slower they run, the closer they can get to Carnot efficiencies. The full design specs are available here. These units can be daisy-chained together, one to the next. The cost of this device is between $180 and $350 USD.
Grid Synchronized Inverter allows you to attach to the power grid. These are now commodity items and the price for a UL Listed 5 kW unit is from $1,000 to $2,500 depending on manufacturer.
System Cost is based on the location and available kWh/m^2/day (kilowatt hours per meter squared per day) on the least sunny month of the year — for me, that is December. According to the NREL solar radiation manual for where I am, 50 miles south of New York City, that is 1.9 kWh/m^2/day. Over the period of a year, the power varies greatly from 1.9 – 6.2 kWh/m^2/day.
3 kW continuous output, over a 24-hour period, with 30% efficiency, requires we gather 240 kWh to produce the 72 kWh this system will produce over the period of a day. One of our design criteria is, we gather 2 – 3 times the power required for a given day. For safety, the further north you go, the higher the multiple should be. For where I am, it is ~2.5, for Texas 1.9 – 2, for Maine 3.0.
Panel Cost
600 kWh = 2.5 x 240 kWh
315.78 square meter = 600 kWh / 1.9 kWh/m^2/day
$10,428 = 315.78 sq meter * $33 per square meters
Other Costs
$1,100 – Thermal Mass (Shipping container or insulated hole in the ground)
$250 – Flow Controller
$200 – Heat Radiator
$250 – LTD Stirling
$1,500 – Grid Synchronized Inverter
$13,728 — Total Parts Cost
NOTE: None of these calculations take into account the reuse and recycling of the energy gathered, by cycling the energy into other zones or thermal masses at lower temperatures. (IE 90 C –> 60 C –> 30 C –> radiator, where “–>” is the LTD Stirling, and the temperatures are of different zones or thermal masses). Above are worst-case calculations.
The thermodynamic efficiency of a solar based LTD Stirling changes based on time of year, and time of day, based on the outside (radiator) temperature. It is not that Carnot takes a holiday (eff not = 1 – tc/th). It is that the temperature differential changes, changing the efficiency. The greater the temperature differential, the greater efficiency of an engine. During the summer months you have a plethora of energy (3x winter), and poor (5%-15%) efficiencies due to a low temperature differential between the heat source and the radiator (outside air). During the winter months you have a high (15%-30%) efficiency, due to the high temperature differential between the heat source and radiator. This allows the system to generate power in the winter more efficiently, with less energy input. It is counter intuitive and thermodynamics at work.
Designing the system based on the day-to-day data for Newark, New Jersey over the same time period, taking into account energy reuse and smart energy management, we can reduce our multiple to 2 and only require 288 kWh worth of panels, reducing the panel cost to $5002.10 USD and the system cost to $8302 USD. With economies of scale and alternate production techniques, increasing the thermal efficiency of the panels (1), further cost reductions are possible, reducing the system cost another ~$3,000 USD, making the system cost approximately $5500 USD. The cost would be lower in southern states like FL, TX, AZ, southern CA.
Total Energy Output over the period of a day is 72 kWh of energy. With a lifespan a 25 years, the total power output is…
657,000 kWh = 25 year * 365 days * 24 hours * 3 kWh
657 MWh total energy produced over the lifespan of the Stirling.
Levelized Cost of Energy or LCOE is basically the the cost of the generating plant, fuel, and maintenance over its life span — minus subsidies — divided by the total energy generated over the period of a generators life span.
The LCOE for the first non-optimized design is $13,728 / 657 MWh or $20.89 USD per MWh. Optimizing just a little brings the LCOE to $8,302 / 657 MWh or $12.66 USD per MWh. Allowing for economies of scale, automation, home building techniques, reduced energy costs in manufacture, and other things this article didn’t have room for, gets the LCOE to $5,500 / 657 MWh or $8.37 USD per MWh.
Summary
Comparing the current cost of energy at ~$100 USD per MWh to a system based on a redesign of a 100 – 200 year old technology shows that sub $20 USD per MWh energy is possible with technology available today. It also shows that renewable energy can be far cheaper than fossil fuels with a little creativity.
David Fuchs is a classically trained engineer and programmer. He is involved in open sourcing, software, and hardware. Current interests: 3d printing and nanotechnology, predicting the future of technology, and low-cost power production in developing nations using material at hand. You can check out his website for more of his writing, and you can contact David on Google +
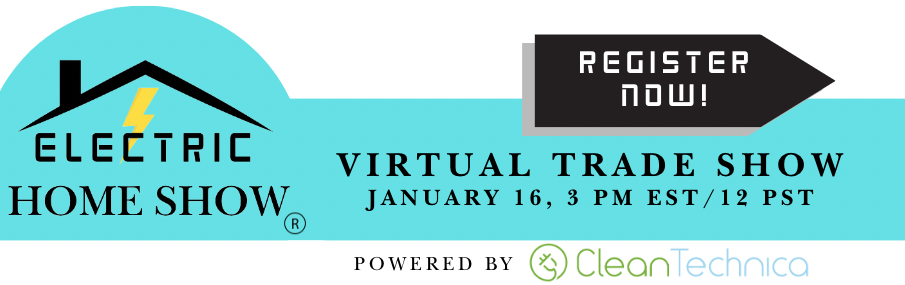
Chip in a few dollars a month to help support independent cleantech coverage that helps to accelerate the cleantech revolution!
Have a tip for CleanTechnica? Want to advertise? Want to suggest a guest for our CleanTech Talk podcast? Contact us here.
Sign up for our daily newsletter for 15 new cleantech stories a day. Or sign up for our weekly one if daily is too frequent.
CleanTechnica uses affiliate links. See our policy here.
CleanTechnica's Comment Policy