Factorial Energy Opens Largest Solid-State Battery Factory In America
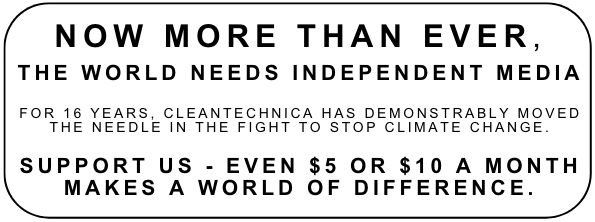
Sign up for daily news updates from CleanTechnica on email. Or follow us on Google News!
If you think about a US solid-state battery manufacturer, QuantumScape is probably the first company that comes to mind. But Factorial Energy has also been pursuing the solid-state battery dream. This week, it announced the opening of its first commercial scale battery factory in Massachusetts, just south of the New Hampshire border.
Factorial Energy has invested heavily in solid-state battery and chemistry research over the past 6 years to create its proprietary Factorial Electrolyte System Technology, which it says is practical, customer driven, and electrode agnostic. The result is the world’s first commercial scale, balanced performance profile solid-state battery cell.
The FEST system has been developed in conjunction with several of the world’s largest auto companies and battery cell manufacturers. It delivers on the promises of solid state performance without the fatal defects found in iterations of the technology to date. The technology will debut in the high spec market as a proving ground for its performance and manufacturability.
In a press release, Factorial Energy CEO Siyu Huang said, “We are thrilled to open our next generation battery facility in Massachusetts as we scale our batteries for mass production. This facility will enable us to manufacture cells to meet the needs of our automotive partners and progress our mission to commercialize solid state batteries. As a U.S. company, we’re also proud to contribute to the onshoring of battery manufacturing for EVs and advancement of battery innovation for a differentiated supply chain.”
The factory in Metheun is near the company’s research and development center and represents a $50 million investment that is expected to create over 150 local jobs. The new factory will have an annual capacity of up to a 200 MWh, which will make it the largest solid-state battery assembly line in the US.
“Factorial continues to drive the battery industry forward and this milestone is no exception,” said Joe Taylor, the executive chairman of Factorial who previously served as the head of Panasonic Corporation of North America. “Automaker demand for American made batteries is high to produce electric or hybrid vehicles that qualify for incentives. Our facility will manufacture automotive sized solid state batteries at pre-production speed and volume, illuminating a clear path to mass production and reaching economies of scale.”
Factorial’s proprietary FEST quasi-solid-state batteries are designed for higher energy density and safety compared to lithium-ion batteries. As Factorial Energy scales up solid-state battery production, the company will continue its commitment to drive sustainability and develop technologies to power the EV revolution.
Solid-State Battery Development And Testing
In a May of 2023 blog post, Factorial Energy lays out the challenges inherent in developing new battery technologies. It says original equipment manufacturers need to follow a clear commercial road map when bringing new technology to the automotive market. It’s a rigorous and lengthy process designed to ensure that customers can rely on the performance of every component of their vehicles, including EV batteries
First, research and development teams test the science behind a new idea. In battery development, these teams often use tiny coin cells in laboratory conditions to test proof of concept. Those tests often show the proposed technology is impractical or non-beneficial, so very few proceed to the next stage. Factorial’s FEST battery is one of the few that has shown both proof of concept and significant benefits over existing technologies.
What works in the lab doesn’t always work in the real world. That’s why manufacturers create several production intent batteries using a certain cell format and capacity, then tests them in laboratories and in real world situations to verify their safety, performance, and functionality. Cell technologies that pass A-validation testing then move to the next development phase or are modified to incorporate the lessons learned in testing. The revised batteries then go through the A-Sample validation process from the beginning again.
In B-Sample testing, the prototype batteries are tested at the cell and module level to optimize their design and to verify their performance in packs and vehicles. Manufacturers and the battery partner can agree to freeze the batteries’ physical design and chemistry and then move to the next phase of development.
With the cell design and materials now set, battery manufacturers begin the process of scaling production to develop a stable process with consistent high quality results. Passing Sample C and D validation certifies the batteries can be produced at reliable production volume and quality.
Once C and D level testing is completed, the battery production line needs to prove it can operate at the intended run rate with a finalized process and quality control plan in place. Those are the cells that ultimately end up in a consumer product like an EV.
Every step of the testing and development process can take several years for the battery to meet rigorous industry standards, guidelines, and regulations from authorities including the International Electrotechnical Commission and the U.N. During the development process, companies are limited to small scale production and have to establish a new supply chain and manufacturing infrastructures. These requirements and challenges have slowed the development of solid-state batteries — but with the right technology, the right policies, and the right partnerships, they don’t have to, the company says.
The Public Policy Piece Of The Puzzle
Factorial Energy says it is excited to see national and international governments adopt policies that allocate funding to emerging EV battery technologies. The United States’ Inflation Reduction Act provides loans and grants to EV battery makers in the US. New EPA emissions regulations and the European Commission’s proposed Battery Passport and Green Deal initiatives also encourage EV adoption.
“Because start-up battery companies cannot do this on their own, we believe the future of battery technology will rely most of all on successful collaboration all along the supply chain between OEMs, automotive manufacturers, and technology developers. For instance, Hyundai Motor Co., Stellantis, and Mercedes Benz have invested in our FEST platform. These partnerships garner not only investment but invaluable support while opening up access to their supply chains as we work towards validating our technology at the cell and module levels,” the company says.
“The growing number of EV technology investments by OEMs forms the basis for solid-state battery developers and manufacturers to overcome current challenges of scalability and cost-effectiveness. This will enable them to take advantage of the exponentially growing market for EV batteries. Valued at $56.4 billion in 2022, this market is projected to reach $134.6 billion by 2027 — a boon for OEMs that may help provide superior solid-state solutions.
“Commercializing solid-state batteries requires innovation, collaboration, and perseverance. We’re eager to realize the potential of reliable, powerful, affordable solid-state batteries to potentially transform the EV industry. With continued investment and innovation alongside our top tier automotive partners, we believe future solid-state batteries will fast-track a new norm of clean, sustainable, electrified transportation. Soon, charging your car before bed will be as mainstream as charging your phone today.”
The Takeaway
Solid-state batteries are expected to be more powerful, lighter, cheaper, and more stable, but there are many companies around the world which are pushing forward with this new technology. In addition to Factorial, QuantumScape and Solid Power are pursuing the dream in the US. Toyota says it is hot on the trail of solid-state battery technology as well, and it’s safe to assume every major battery manufacturer in the world is too.
One of the motivating factors is to find new ways of making batteries that do not involve purchasing battery materials and components from Chinese companies. Although batteries from China are by far the least expensive, the supply chain could face significant disruptions in the event or trade or military conflicts. If that happens, price will take a back seat to availability.
Deliveries of batteries from Factorial Energy are probably several years away. In the race to develop solid-state batteries, it is impossible today to know who the winners will be tomorrow.
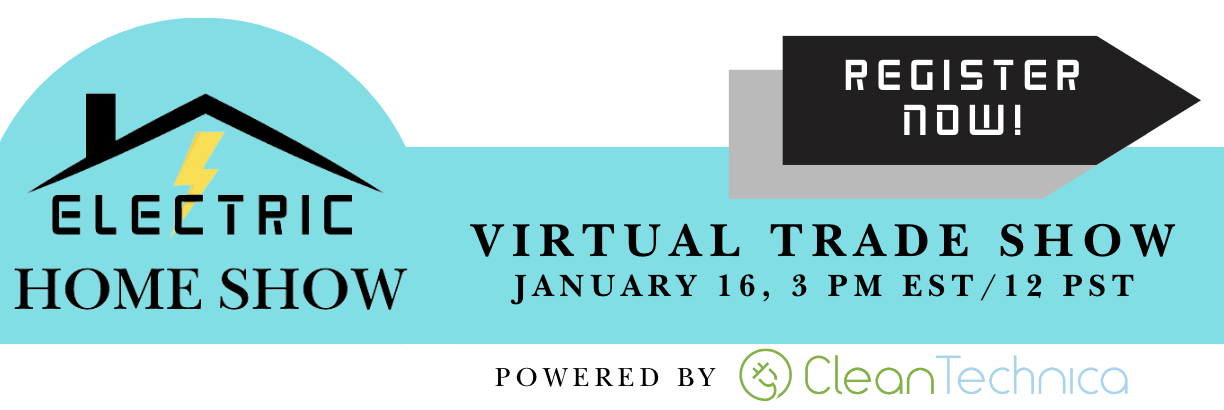
Chip in a few dollars a month to help support independent cleantech coverage that helps to accelerate the cleantech revolution!
Have a tip for CleanTechnica? Want to advertise? Want to suggest a guest for our CleanTech Talk podcast? Contact us here.
Sign up for our daily newsletter for 15 new cleantech stories a day. Or sign up for our weekly one if daily is too frequent.
CleanTechnica uses affiliate links. See our policy here.
CleanTechnica's Comment Policy