Taller Wind Turbines To Get TLC From 3D Printing
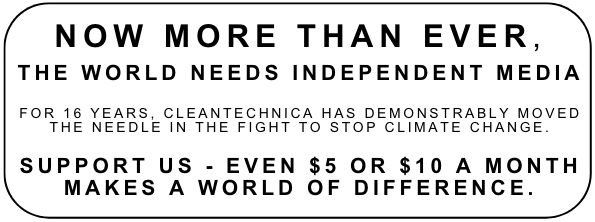
Sign up for daily news updates from CleanTechnica on email. Or follow us on Google News!
Vast swaths of the US have yet to be tapped for wind energy, partly on account of politics and partly because wind speeds in those areas are less than optimal. Only the voting public can take care of the political end. Meanwhile, engineers and innovators are hammering away at the wind speed issue, which can be solved by building taller wind turbine towers. That’s not as easy as it sounds, but GE Renewable Energy is banking on 3D printing to overcome the obstacles.
Why Not Taller Wind Turbines?
Taller wind turbines have several advantages over their shorter cousins. They can reach heights where winds are stronger, without interference from trees, topography, or buildings. The greater height also allows for longer blades, which means a single turbine can harvest more energy. The cost efficiencies can also pile up for taller, longer wind turbines, at least on paper.
There being no such thing as a free lunch, the cost factor can also pile up, and not in a good way. Transporting long sections of conventional steel tower can be a deal-breaker on account of logistics alone, making it impossible to construct taller towers where road curvature and other infrastructure pose obstacles. Similar obstacles present to prefabricated concrete bases that would be large enough to support a taller tower.
Pouring the concrete on site would solve the transportation issue, but it raises new headaches for project managers who are tasked with assembling a crew in a remote location and keeping them there for as long as it takes to construct the tower.
Taller Wind Turbines & 3D Printing
One solution to the problem is modular construction. The global wind energy firm Vestas has been applying that approach to the nacelle, which is the energy transfer system that sits atop the turbine tower.
The modular approach has been catching on in the turbine tower area as well, and GE is bumping things up a notch by adding 3D printing to the mix. The idea is to transport the printer to a site and print the concrete base right there. With only a few people needed to operate the printer during this stage, labor costs become more manageable.
GE recapped its previous work on the 3D printing project back in 2020, and it was quite enthusiastic about partnering with the 3D printing leader COBOD and Holcim (formerly LafargeHolcim), the sustainable building firm.
“Ever since Charles Brush built the first wind-powered generator in Cleveland, Ohio, in 1887, engineers have been looking for a practical way to squeeze more power out of wind turbines, stretching their blades and making them grow taller. Now a combination of 3D printing, materials science and robotics could unleash a new growth spurt for the industry,” GE enthused.
The Repowering Solution
Considering the obstacles faced by wind turbine developers in many US states, one might ask why GE is bothering to push for higher wind turbines. The answer could be pretty simple. Even if some states stubbornly resist new wind turbines, there are plenty of opportunities to be had in repowering old wind farms.
Thousands of existing wind turbines in the US are already beginning to age out, and wind energy stakeholders are already beginning to upgrade them with more powerful turbines.
The turbine repowering trend is even hitting wind farms that are still in the planning stages, enabling developers to drop their costs by reconfiguring their arrays to accommodate fewer turbines.
Add taller towers to the mix, and the payoff for repowering old wind farms could be irresistible.
According to GE’s figures, the improvement is significant even without a turbine upgrade. The company calculates that the average 5-megawatt turbine generates 15.1 gigawatt-hours annually at 80 meters high. The same turbine could generate 20.2 gigawatt hours at 160 meters high
Wind Turbines: How High Can They Go?
As of 2020, GE noted that the tallest onshore wind turbine clocked in at 178 meters. They were referring to a “water battery” that piggybacks pumped hydro energy storage into a concrete wind tower base. It’s an interesting concept for leveraging more cost-effective renewable energy in hydropower sites, though its application would be limited to sites with water resources.
GE is betting that 3D printing will provide for a more expansive array of sites while cutting costs, eyeballing a height of 150-200 meters.
COBOD’s contribution is the design of a 3D printing system that can be transported to a site.
“Once there, the system will suspend a printhead from an elevated track like a magic marker with a tip the size of a gallon milk jug. The tip releases the concrete through a print nozzle as it follows its programmed course,” GE explains.
Holcim came up with the concrete blend that stiffens quickly, but not quickly enough to clog the nozzle.
World’s Largest 3D Printer Of Its Kind
To be clear, GE’s tower design is not concrete throughout. The key to the design is a concrete base, which will support a longer section made of steel tubes. The steel part is flexibly engineered to absorb wind, like a modern skyscraper.
GE also designed the steel tower to be tailor-able. Its height can be adjusted according to the wind developer’s needs.
As of 2020, GE and its partners passed one of their major milestones, which was the 3D printing of a concrete base 10 meters tall. The next goal is 20 feet, and they have just announced the ribbon-cutting on a new 3D printing facility that will get them to that level.
The new 3D printer is no small potatoes. It is the height of a three-story building and is billed as the largest of its kind in the world. Here, let’s have Henrik Lund-Nielsen, the founder and General Manager of COBOD, explain:
“The printer we have delivered is second to none: not only can it print in excess of 10 tons of real concrete per hour, but in addition, it is the first 3D concrete printer in the world with two X-axes on the printer. With the multiple functions of the printer, the printer can better be described as a multifunctional construction robot than a printer.”
GE is not shy about checking into new ideas for increasing wind turbine efficiency. Some of them haven’t had a widespread impact, such as new cladding for grid-style towers and wind-breaking covers for nacelles. However, its offshore mega-sized offshore wind turbines have set the offshore industry buzzing. If all goes according to plan, the 3D printing could change the game for onshore wind development, too.
Follow me on Twitter @TinaMCasey.
Photo: 3D printing for wind turbines courtesy of GE (via email).
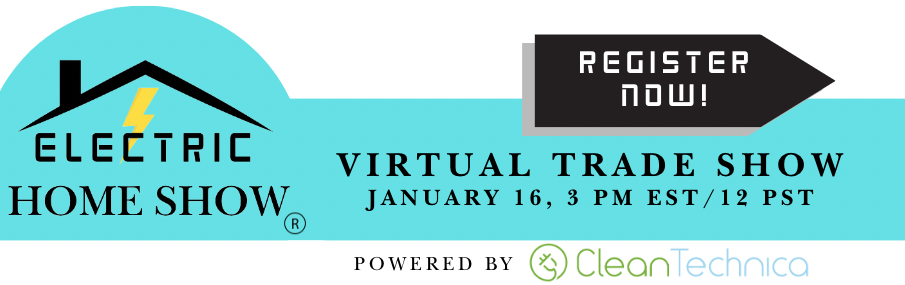
Chip in a few dollars a month to help support independent cleantech coverage that helps to accelerate the cleantech revolution!
Have a tip for CleanTechnica? Want to advertise? Want to suggest a guest for our CleanTech Talk podcast? Contact us here.
Sign up for our daily newsletter for 15 new cleantech stories a day. Or sign up for our weekly one if daily is too frequent.
CleanTechnica uses affiliate links. See our policy here.
CleanTechnica's Comment Policy