EV Battery Swapping Will Have Some Big Niches But Mostly Won’t Be Used
Every time I publish anything on electric vehicles, the battery swapping fans come out of the woodwork. It’s remarkable that there is barely any battery swapping being done with electric vehicles today and yet some people think every EV of every scale will be treating the most expensive component as a chunk of kit they will swap with strangers. They trot out videos of battery swapping occurring or reference NIO as if examples were data.
This happened again after I published on why dirt cheap batteries make it possible to charge a lot more freight trucks a day without big grid upgrades that can take years. In geographies with weak grids and sluggish utilities like the USA, cheap behind-the-meter batteries can be pulling grid energy 24 hours a day and dispensing it at fast-charging power levels when trucks roll in. With CATL announcing that $56 per kWh LFP batteries will be available in Q4 of this year, all economic modeling of truck charging has to be redone.
With $30 likely in 2030, swapping 24 hours of energy for a couple of hours of power instead of upgrading the grid makes broad economic sense. But cheap batteries don’t float all battery use case boats, with swappable batteries being a case in point. This doesn’t mean that there won’t be battery swapping use cases, but they’ll be in specific niches.
Let’s start with the pros and cons of battery swapping. On the plus side of the equation, the vehicle returns to service in minutes instead of more minutes. I say that very carefully, because battery swapping people seem to think that only achieving diesel truck or gas car refueling rates will be acceptable the vast majority of the time, and they also seem to think that charging takes hours.
Except, even megawatt-scale charging doesn’t take hours and a large percentage of trucks are parked at night, so slower charging is just fine. As an example of the first, China’s Windrose Technology and its partners, including BorgWarner New Energy (Xiangyang) Co., are delivering a 49 ton total truck — that’s 13 tons more than a Class 8 truck, with a 1,000 km range and megawatt-scale charging that can add 400 kilometers of range in 36 minutes. That’s pretty close to mandated rest times for drivers even in the USA.
Semi trucks in urban areas often spend the night in depots, where a bunch of trucks can be charged slowly. So do buses. So do airport ground vehicles. While ports in the rest of the world operate around the clock all year long, US ports have two eight-hour shifts and one five-hour shift Monday to Friday, and ports avoid running on weekends and during that missing three hours because overtime is expensive.
I’ve looked at electric bus fleets globally and have found exactly no examples of any operator using swappable batteries, just static charging and sometimes dynamic charging — while the bus is in motion from overhead or road-embedded electricity — where it pencils out as a requirement. Bus fleets run 18 to 20 hours every day, with the buses away from the depot the entire time, so if swapping batteries made sense, battery fleet operators would be swapping batteries. They aren’t stupid and do know how to use spreadsheets, just like every other fleet operator. Unlike personal vehicles, total cost of ownership calculations are lifeblood for fleet operators because it’s a low-margin business.
The people who build electric buses aren’t stupid and are spreadsheet-competent too, so if it made good economic sense and they could sell more bus systems, they would be doing that. They aren’t.
What are the downsides to battery swapping? One of the biggest is that anytime you are removing a big chunk of something from a vehicle and replacing it, there’s an opportunity for something to go wrong mechanically and there’s wear and tear on all connections. Plugs need to be aligned and go in squarely, pins on plugs get bent or shoved in, the big chunk of stuff gets dinged off of a wall and gets out of alignment or stops working until fixed, and you need more spare batteries and trucks as a result.
One of the huge advantages of battery electric trucks is that they have a lot fewer moving parts that can go wrong, and swapping batteries decreases this advantage. All else being equal, swapping batteries increases maintenance costs. A single big plug for a charging system is much less likely to go wrong.
One example that someone shared was an Australian system which involved a forklift operator pushing metal prongs through slots in the battery stack, lifting it a couple of centimeters and then backing slowly away from the truck. The reverse process put charged batteries into the truck. Not calling out forklift operators or anything, but 50% of all operators finished in the bottom half of their forklift class and batteries are probably going to be the most expensive thing they move. Accidents will happen.
Batteries are best left where they are, whether that’s in the frame of the truck or in a shipping container full of them buffering electricity.
Chip in a few dollars a month to help support independent cleantech coverage that helps to accelerate the cleantech revolution!
Swappable batteries also have to be packed precisely for the hole in the specific vehicle. The vehicle has to be engineered with fail safes for removal and installation of the packs to reduce the problems outline above. Both add constraints. Meanwhile, a buffering battery is a shipping container or two that is delivered, plugged in, tested and then just sits there as a solid state lump of metal and chemicals charging and discharging.
The cheapest form of battery storage is the one that’s assembled in a shipping container in China, delivered to a site by standard transshipment logistics ships, trains, and trucks, and placed gently on a slab of concrete that’s been poured for it, then plugged in and left alone. That gives them the best possible operating conditions under the easiest to monitor conditions.
Batteries in trucks and buses are more expensive than that because they have to fit into the chassis and deal with constant vibration and rattling. It’s not nearly as big a problem for batteries as for fuel cells and all of the high-precision bits and bobs that come with them, but a battery pack engineered for a truck or bus has higher requirements and lower unit scale than a bunch of batteries and electronics put into a shipping container with a plug in a factory. Once again, this is not a show stopper for swapping, but another factor in the total cost of ownership calculation.
Swappable batteries also create another challenge, which is inventory. It’s not a big challenge, but it becomes one if you have a big fleet. The batteries have to have a place to sit in the facility that’s accessible, can have a lot of batteries moving in and out of it, and have power connections, monitoring, and fire safety systems. A big containerized buffer battery will just sit outside somewhere convenient and wires will bring electricity to chargers. The latter is simpler most of the time for most use cases.
Moving electricity between batteries from different manufacturers in different vehicles is as easy as standardizing on the plug, as has happened with the NACS plug in North America, where Tesla’s market dominance for EV charging made it sensible to adopt its plug as the standard. But swappable batteries require standardizing battery packs across all manufacturers who make trucks or buses that will use the charging station.
For truck stops specifically, the trigger this time for the people who love the idea of battery swapping, this won’t play out well. Every truck manufacturer would have to agree on the same exact standard for battery packs. There would likely have to be battery packs for three or four classes of trucks. There would have to be automated battery swap systems that could handle three or four classes of trucks. There would have to be a big battery storage and charging shed built with racks for three to four different types of batteries and some automated pick and deliver system to move a charged battery from storage, across the lot to the truck and slot it into the truck.
One of the observations that I make is that enthusiasts for specific technologies often aren’t good systems thinkers. They see a specific constraint (charging time in this case), leap to the solution that occurs to them (battery swapping), and don’t proceed to work out what that would look like in real-world operation end to end. This doesn’t make them bad people or necessarily incompetent at what they do, but enthusiasts who don’t think things through can be annoying, and as with the hydrogen for energy crowd, they waste a lot of time and money. At least the battery swapping enthusiasts aren’t backed by the oil and gas industry.
The combination of all of the above means that battery swapping with the same MWh as battery buffering will be more expensive in capital costs and more expensive in terms of operating costs, most of the time. This doesn’t mean it won’t pencil out in specific places.
Reading this, you might be surprised to find out that I’m bullish on swappable batteries for shipping and trains. I’m bullish on containerized batteries for that use case simply because everything else required for them is already in place, unlike other battery swapping solutions.
- Cranes, reach stackers and straddle carriers to pull containers on and off ships and trains? Check.
- System that already plug containers (reefers) in on shore and in ships or trains? Check.
- Security controlled place to store containers of batteries? Check.
- Container control systems that keep track of every container, its special needs if any and where it is? Check.
- Batteries built into containers at factories already? Check.
- Logistics system built around things that size and mass? Check.
- Big volumes of ships, trains and containers so room for optimization? Check
- Already happening on 700 unit container ships in China? Check.
When we scale to the size of ships and trains which move containers already, swappable containers of batteries start to make more sense. Ships that run on a scheduled route between ports and carry containers — ropax ferries and most inland and short sea container ships — and all trains with their fixed rails and their freight yards that carry freight too and from ports are an obvious place to swap cheap containerized batteries. Everything is already there.
Further, my projection expects that long haul shipping will optimize around hybrid systems with biodiesel for crossing much of the distances and batteries for national waters and when berthed in ports. That pushes noise and air pollution away from people and most other things, as well as being cost optimal. In 2022, a study published in Nature found that at US$100 per kWh, battery electric freight shipping was economically competitive up to 1,500 kilometers. At $50, which is about what CATL will be shipping in Q4, 3,000 kilometers. That’s the distance across the Atlantic between Newfoundland and England, for context.
But to be clear, train batteries aren’t required everywhere, only places where there isn’t an overhead catenary line and it’s too expensive to add one. Rail is being electrified with overhead catenary connections everywhere in the world except North America, and a container-sized Tesla Megapack storing 3.9 MWh of juice will only move a relatively short, 950 meter train with maximum mass carrying cars 10 kilometers up a maximum 2% grade. But if a rail line wasn’t built for electric from scratch, tunnels and bridges are expensive, often very expensive, to add lines to.
Sufficient battery energy to power trains across gaps in overhead connections will usually pencil out as the most cost effective solution. A couple of data points support this. First is the excessive cost of rail electrification in the UK, where powering bridges and tunnels has tripled the cost per kilometer for the system. Betting on batteries would have cut electrification infrastructure costs by two-thirds. The UK has been seeing £2–£2.5 million per kilometer costs to electrify its rail compared to European countries that built it that way to start with seeing under £500,000 per kilometer.
The second data point is the rail study out of the German state of Baden-Württemberg, which did a total cost of ownership study across grid-tied, battery and hydrogen trains, and found that batteries made a lot of sense, being only slightly more expensive than grid tied where ranges were viable and the rail wasn’t already electrified or expensive to do. Hydrogen was three times as expensive, of course. Interestingly, plummeting battery costs means longer routes are becoming viable for at least passenger trains without any concerns.
Rail in Europe is overwhelmingly passenger rail, so the transposition isn’t perfect, but India will have 100% of its heavy freight rail, the mode which carries about 75% of India’s domestic freight, electrified this year, China’s rail is about 75% electrified right now, including its high speed freight on the new tracks and the China to Europe freight rail connection which is carrying an increasing percentage of cargo these days.
So trains and ships make sense for battery swapping due to everything already being worked out except the business model, which won’t be as difficult because there are so many fewer players than for truck stops. Energy as a service in containers will be easy to sell to big shipping and rail firms, but standardizing all Class 8 trucks from every vendor for battery packs is a very big barrier to success, as is building battery swapping and storage at truck stops.
But there are other places where battery swapping will pencil out. The conditions for success are mostly the ones that shipping and rail have with containers. A fleet operator with a geographically constrained range, operations which are 24/7/365, existing freight location management solutions and freight movement operations staff have a choice.

Have a look at this total cost of ownership study that APM Terminals, the port concessions operations arm of Maersk, did with the assistance of the NEON group at Eindhoven University of Technology. I talked with Sahar Rashibeigi, head of decarbonization for APM Terminals, a couple of times last year about this.
A couple of things leap out. The first is that the vehicle cost for battery electric vehicles is already going to be lower due to plummeting battery costs, and the gap between diesel and battery vehicles may have disappeared already.
The second is that downtime cost. That’s charging time, and includes an increase in the number of vehicles that are purchased for ports for the same workload. Where there’s actually a 24/7/365 workload, frequently more vehicles are required for the same service load.
Ports are a place where an organization like APM Terminals could settle on a single vehicle provider for all of the port vehicles and make battery swapping work. The combination wouldn’t be as expensive as buying new vehicles. Remember that it’s the USA where port work is a 21 hour a day, five day a week job, not the rest of the world.
However, that runs into a different problem. As Rashibeigi told me, there are only about 120,000 reach stackers, straddle carriers, and terminal tractors running around the 900 or so major ports in the world. It’s a very small number of vehicles compared to the 4 million Class 8 trucks in the USA alone. The market is also fragmented, without a dominant OEM for the space. I’d suggested to Rashidbeigi that Maersk should partner with the biggest one or two OEMs for port vehicles and make them the de facto supplier for port equipment to drive cost savings through scaling by numbers into the space.
As it is, that fragmentation means that ports will have vehicles from multiple manufacturers, that the manufacturers don’t have sufficient scale to engineer and design battery swapping systems as well, and that it’s just going to be easier and cheaper to oversize batteries in vehicles, put in faster charging, buy fewer additional vehicles as a result, and put in buffering batteries. It’s unlikely ports will see battery swapping, in other words.
Big distribution centers like Amazon’s, where legacy oddities from historical US DOE incentives see the US having the majority of the tiny number of hydrogen forklifts globally, are a place where battery swapping could make sense. By definition, big warehouses full of shelves, lots of operations staff, secure conditions, fire monitoring, a warehouse management system, a lot of exactly the same vehicles doing exactly the same job, 24/7/365 operations, and the like. An automated battery swap system for forklifts might make sense economically in a big distribution center, and millions of forklifts are sold annually, unlike port vehicles. It’s a big enough market. Unsurprisingly, when I just checked, multiple manufacturers are offering that.
I noted the other day regarding the emergence of standardized, swappable, 2-cubic-meter roro boxes for urban electric cargo trike systems which include an electric trike with an open frame which the box can be secured in, 3-5 cargo boxes on wheels which will be filled at depots and even trucks optimized for the roro boxes to shuttle them around. This is another place where swappable batteries might make sense, potentially built into the bottom of the roro boxes themselves. When the boxes are in the trucks or in the depot, they can be charging and the electricity delivered to the cargo trike wherever it happens to be. All of the components necessary for battery swapping are already in place, it just needs some spreadsheet work to see if it makes sufficient sense, and I’m sure the providers of complete systems have done that math.
Rapid-turnaround-time, high-power-intensity applications are another place where battery swapping is de rigeur. Heavy-lift drones use a lot of energy in a short period of time. Agricultural seeding and spraying drone systems have drones up to 4.3 meters in diameter, carrying up to 90 kilograms of product per flight, with flights lasting ten minutes for a pass, and systems all come with swappable batteries. As the hopper is being filled with product, the used batteries are taken out and dumped in the charging rack on the trailer and fresh batteries are slotted into the drone for the next pass. Same thing with tree planting drones.
Both of those drone applications are radically lower cost than the approaches that they replace, and swapping batteries makes strong economic sense.
I suspect that many people who love the idea of battery swapping for EVs work with modern power tools a lot. Powered hand tools have switched to batteries wherever possible because it’s such a good application, but batteries don’t last a work day. A few swappable batteries that charge while the hand tools are being used or overnight makes complete sense. Because it’s familiar to them, the people I’m thinking of think it’s more broadly applicable than it is. It’s certainly the only reason I can think of to explain the legions of battery swapping fans I encounter every time I publish on EVs and freight logistics.
After all, pretty much everybody in the world above the harshest poverty line is used to plugging in devices with their own, non-swappable batteries. That’s about as familiar as it gets, yet the number of people excited by battery swapping is out of all proportion to its economically viable use cases.
Have a tip for CleanTechnica? Want to advertise? Want to suggest a guest for our CleanTech Talk podcast? Contact us here.
Latest CleanTechnica.TV Videos
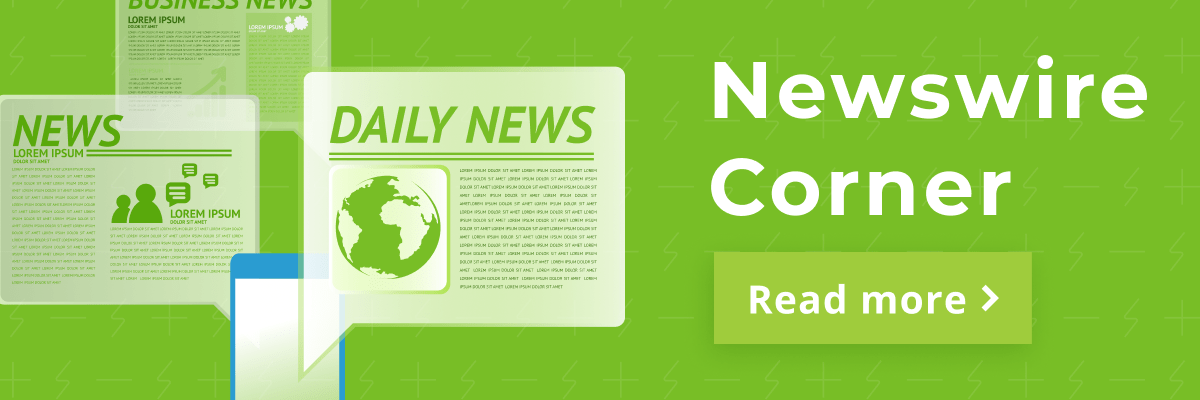
CleanTechnica uses affiliate links. See our policy here.